Portable Sump Cleaners for CNC Coolant and Metal Fines Recovery
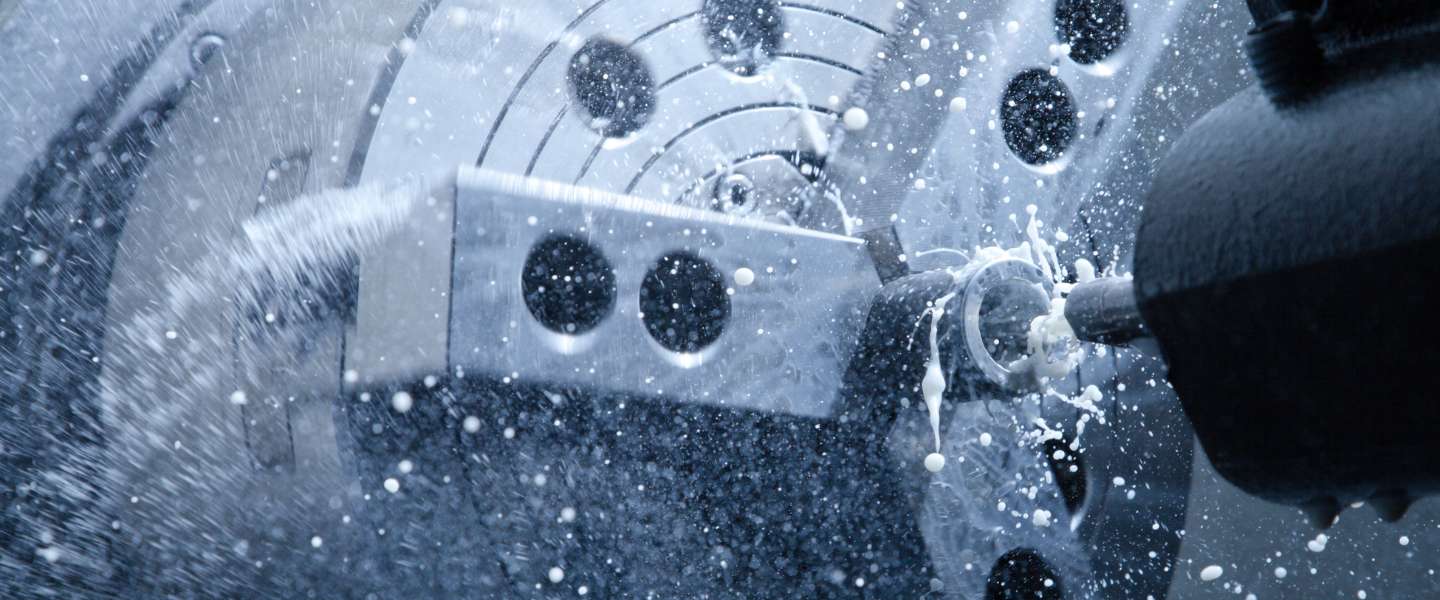
Clean Machine Sumps Quickly With The Green Machine Coolant Recovery Vacuum Cleaner
In the precision-driven world of CNC machine shops and manufacturing facilities, the health of coolant systems is paramount. Sump suckers emerge as a critical ally in this context, offering an efficient solution to a common yet overlooked problem—coolant contamination. As an integral component of industrial fluid management, our portable coolant vacuum cleaners ensure the continuous removal of metal shavings, sludge, and other particulate matter from coolants & cutting oils, directly contributing to the optimal performance and longevity of machining operations.
Coolants & cutting fluids play a dual role in manufacturing processes, providing necessary lubrication and heat dissipation for cutting tools and workpieces. However, their effectiveness diminishes with the accumulation of contaminants, leading to potential machine malfunctions, decreased tool life, and compromised product quality. The proactive removal of these impurities through effective sump cleaning is, therefore, not a convenience but a necessity.
The Green Machine & Green Machine DTS are an economical and compact solution to these challenges, requiring only 19 cfm of air to operate. It efficiently filters fluids down to 50 microns, facilitating the easy transportation and discharge of contaminated fluids to a recycling station or waste containment area.
Designed for simplicity, the Green Machine comes as a complete, turnkey system, equipped with everything necessary for the rapid removal in 15min or less of contaminated fluid from machine sumps or washer reservoirs, ensuring hassle-free startup and easy operation.
The Green Machine
Specifications and Applications:
- Operates on compressed air, requiring no electrical power
- Features a 55 or 90 US gallon capacity, catering to a variety of sump sizes
- High-suction capability of 55-70GPM to remove coolants/oils, sludge, and metal fines quickly
- Made to Fit Narrow Spaces: Ideal for small to medium-sized machine shops
- Air Venturi Suction/Discharge Feature
- Heavy Duty Casters: Lightweight and easy to maneuver, it can be used across multiple machines within a facility
- 50-200 Micron Filtration Bags
- Tool Holders & Forklift Guides
- 1 cu.ft. basket
- Pumping Rates of 55-70 GPM
- 8” x 8” Clean Out Discharge Door
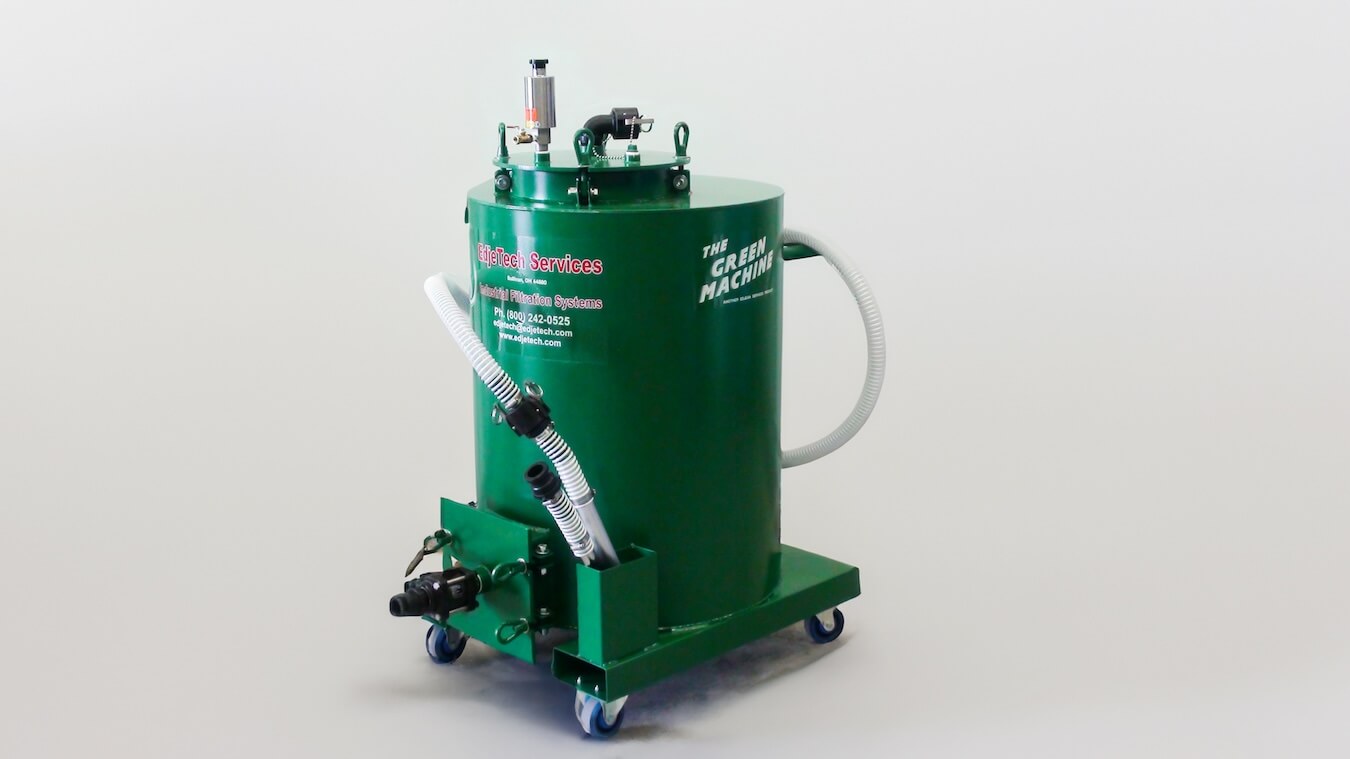
The Green Machine DTS (Dual-Tank System)
A dual tank system with an extra tank that holds clean fluid for quickly recharging the machine reservoir with clean coolant.
Specifications and Applications:
- Operates on compressed air, requiring no electrical power
- Features a 55 or 90 US gallon capacity, catering to a variety of sump sizes
- High-suction capability of 55-70GPM to remove coolants/oils, sludge, and metal fines quickly
- Made to Fit Narrow Spaces: Ideal for small to medium-sized machine shops
- Air Venturi Suction/Discharge Feature
- Heavy Duty Casters: Lightweight and easy to maneuver, it can be used across multiple machines within a facility
- 50-200 Micron Filtration Bags
- Tool Holders & Forklift Guides
- 1 cu.ft. basket
- Pumping Rates of 55-70 GPM
- 8” x 8” Clean Out Discharge Door
Understanding Sump Suckers
Sump suckers typically employ a straightforward filtration mechanism to separate contaminants from coolant and cutting oils during the cleaning process. This may involve a basic strainer or screen to capture large particles and debris, preventing them from being reintroduced into the machine's coolant reservoir.
The primary function of sump suckers is to remove the mixture of coolant and solid contaminants efficiently, rather than performing fine filtration. After the extraction, the coolant can be treated or filtered further if required, using additional filtration solutions to ensure its purity before reuse or disposal.
These powerful vacuum systems are engineered to maintain the cleanliness and integrity of coolant and cutting fluids, crucial for the optimal performance of CNC machines, lathes, mills, and grinders.
How Sump Cleaners Work
The operation of a sump sucker is straightforward yet highly effective. It uses a high-suction vacuum to draw out the mixture of coolant and contaminants from a machine’s sump. The liquid is then passed through a filtration system within the sump sucker, which separates solid waste and contaminants—such as metal particles, sludge and tramp oils—from the coolant/cutting oil. The cleaned coolant can either be returned to the machine’s sump for reuse or properly disposed of if it’s beyond recovery, while the solids are compacted for easy disposal.
This process not only conserves the coolant by extending its usable life but also reduces the time and labor typically involved in manual sump cleaning methods down to a simple 10-15 minute cleanup.
Key Components
- Vacuum Generator: Creates the suction power necessary to extract fluids and solids from sumps.
- Strainer or Screen: Captures larger solid contaminants during the suction process to prevent them from reentering the coolant system.
- Storage and Separation Tanks: Collects the extracted mixture, allowing solids to settle or be filtered out before the coolant is either returned to the sump or transported for disposal.
- Discharge System: Enables the cleaned coolant to be pumped back into the machine sump or disposed of, completing the cleaning cycle.
FAQs
Absolutely. The Green Machine and its DTS counterpart are versatile enough to handle a wide range of coolants and cutting fluids, from oil-based to water-soluble emulsions, ensuring optimal recovery and filtration across many different machining operations.
The Green Machine DTS significantly reduces the time and labor involved in sump cleaning, from potentially hours down to minutes, without interrupting the machining process. Its dual-tank system enables simultaneous sump cleaning and coolant replenishment, minimizing machine downtime.
Choosing the right model depends on several factors, including the size of your facility, the number of machines in use, and the volume of coolant to be managed. Our team can help assess your needs to recommend the most suitable system, ensuring you get a tailored coolant management solution.
Yes, our systems are specifically engineered to tackle heavy loads of metal fines and sludge, ensuring thorough cleaning and filtration. This capacity is vital for maintaining coolant quality and preventing machinery wear and tear.
Reduce Waste & Boost Productivity
For over 38 years, EdjeTech Services has engineered advanced fluid filtration and recycling solutions for machining and metalworking industries.
Our systems increase uptime, cut costs, extend fluid life, and improve efficiency. Discover how we can optimize your operations today.
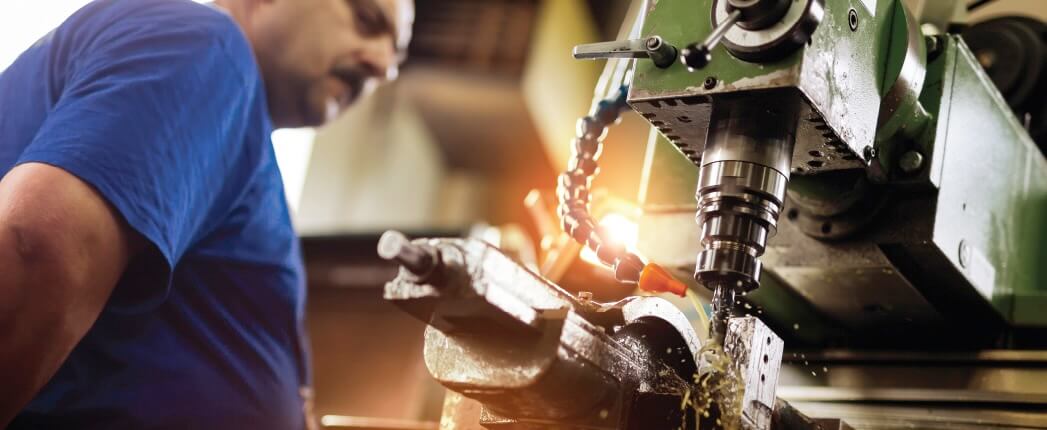