FAQs
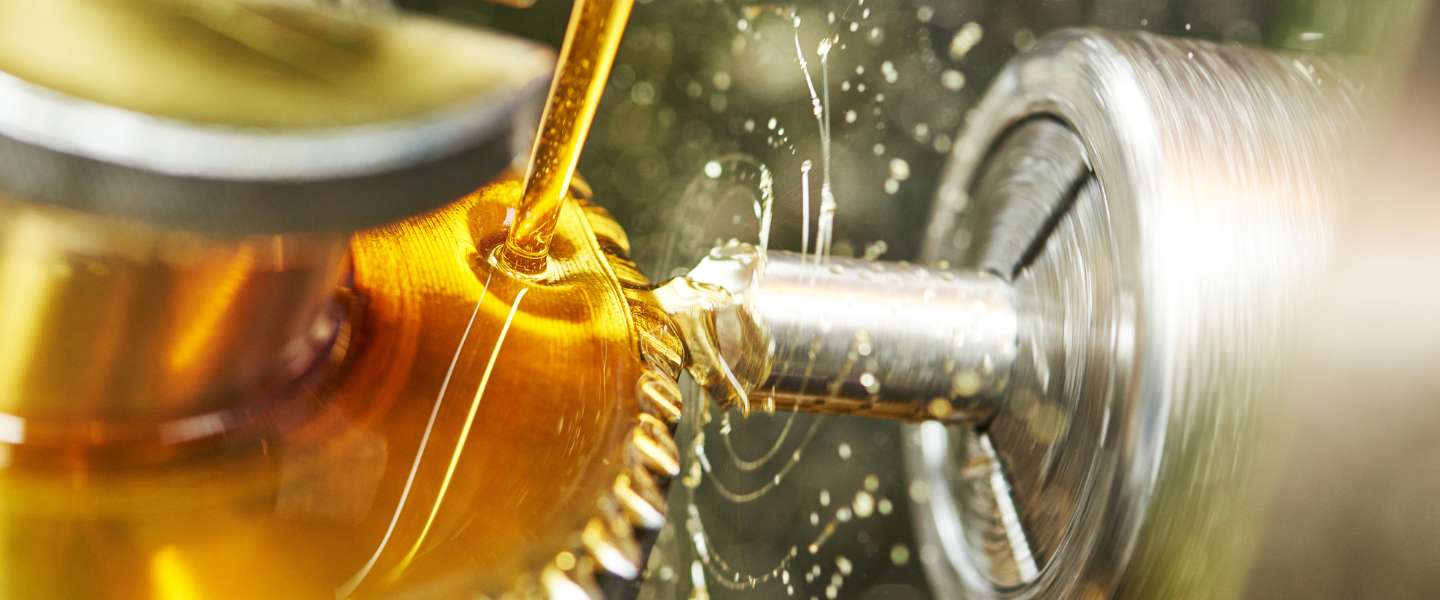
What is an Oil Skimmer?
An oil skimmer is a machine that is used to remove oil floating on the surface of another liquid. There are two basic options in this type of technology, one that is used for large surface areas, such as oil spills in lakes or large bodies of water like oceans, or smaller units that are designed for use in industrial applications.
The most common use for oil skimmers in industrial or processing types of applications is removing the oil from machine tool coolants or collecting oil from the surface or systems designed to clean parts and components. They are also commonly used to remove oil before the liquid is moved to chemical waste treatment systems. By removing the oil from the surface of the water or coolant, it extends the duty cycle for the liquid as well as allowing for better and more consistent performance with multiple cycles.
Additionally, the use of the oil skimmer promotes compliance with the disposal of liquids from these systems or after the duty cycle of the liquid is reached.
How does an oil skimmer work?
There are different options and designs in oil skimmers on the market. Skimmers can be designed to use a Weir method, which has the water flow over a dam type of configuration where the oil floating over the surface runs over the weir and is collected.
Other design options include a belt design, which allows a belt moved across the surface to absorb and push floating oil into a collection area and off of the surface of the liquid to be recycled.
Oleophilic systems are similar in that an oleophilic device, which is often a drum or disc, passes over the surface of the liquid. The collection device then passes through a cleaner and the collected oil is captured with very limited amounts of the liquid. A non-oleophilic system can also be used, which allows a metal skimmer to replace the rope, disc or drum.
The most efficient oil skimmers employ coalescing media. This oleophilic media attracts mechanically dispersed oil droplets causing them to float to the surface of the fluid where they are skimmed off and disposed of. The clarified fluid is returned to the process immediately.
How does an Oil Water Separator Work?
There are many different options in oil water separators. The design of the system varies based on the needs of the application, including the volume of liquids to be processed and the speed at which the separation needs to occur. Smaller units are designed to work with a specific machining system, extending the duty cycle of the coolant.
There are also different separators used in different industries. A key factor in the design and choice is the type of oil or contaminant that needs to be removed. This may include free-floating oil, dissolved oil, mechanically dispersed oil, and even oil that may contain suspended types of solids.
Based on the oil droplet size, the density, temperature and viscosity, the rate of feed of liquid to be treated and the desired end quality of the discharge water/liquid, different systems are more advantageous and efficient.
The basic operation of the oil water separator is to use a skimmer to remove the free-floating oil on the surface. This liquid, with the free-floating oil skimmed from the surface, is then pumped into a tank in the system.
The tank has a solid filtration system, a coalescing chamber as well as a tramp oil trough and a weir to drain off overflow and control the volume of fluid in the tank, preventing any of the coolants from being pushed into the tramp oil trough. The filtration system removes larger droplets and particles, with the coalescing chamber designed with a finer filtration system to trap the smaller sized droplets, coalescing them together until they create a larger oil droplet that floats to the surface.
Highly efficient and easy to operate on equipment, the use of an oil water separator extends the life of cooling fluids and helps to reduce overall costs in machining shops and other similar types of applications and industries.
Why Should I Filter Machine Coolants?
In any type of industry where machines and equipment use coolant liquids, having the ability to extend the life cycle of the coolant is important. This includes machining equipment such as grinders, horizontal and vertical machine centers, lathes and parts washers.
There are several important reasons to filter this coolant on a regular basis. Having an oil and water separator to filter the liquid will benefit any business by:
- Reducing costs – By using an oil water separator and filter system, machine-dispersed, free-floating, and tramp oil, as well as suspended solids, can be efficiently removed from the liquid. This allows the liquid to be used to the maximum duty cycle, helping to reduce the costs associated with draining and replacing the coolant due to the buildup of oil and solids.
- Less waste disposal – In addition to reducing the costs of replacement of the coolant, by filtering rather than replacing, the business has lower waste disposal costs. Small amounts of removed oil and solids are more economical to dispose of as compared to completely draining the system and getting rid of the dirty coolant.
- Long life cycle of equipment – By keeping the coolant filtered, the equipment has a longer life cycle. Without the tramp and mechanically dispersed oil, as well as the associated suspended solids in the liquid, the equipment is more effective and efficiently cooled, preventing problems that occur from inefficient cooling during operation.
- Top ROI – Investing in an oil water separator and filter systems for coolant is not an investment that takes a long time to pay for itself. In fact, in most types of machining and part-washing equipment, effective industrial filtering systems pay for themselves in about four months of use. The more the systems are used, the faster they pay for themselves and start saving the business money.
How To Remove Tramp Oil from Coolants?
The tramp oil is the oil that floats on the surface of the machining or wash water tank and is generated through the use of metalworking equipment as well as in different processes. This oil can also be called sump oil, and it is problematic as it limits the effectiveness and the life of the coolant. It leads to costly equipment breakdowns and causes cutting tool wear if not removed from the coolant on a regular basis. Excessive amounts of tramp oil can lead to smoking, cause issues with coatings, coat cabinet windows, increase bacteria, increase fungus, and reduce coolant pH creating the production of acids that destroy the surfaces of metal parts on equipment.
Removing tramp oils can be done via several different processes. The most effective is a coalescing filter system that removes these oils from the coolant. A pump on the system pulls the liquid from the coolant tank of the equipment. This liquid goes into a reservoir on the separation system where the coalescing media removes droplets of surface oils as well as mechanically dispersed (beaten in) oils. There is also a bag filter that removes solids from the coolant. The removal of dirt and free oils from the reservoir creates a positive environment which increases coolant life, and helps maintain pH, concentration, and bacteria levels.
The free oils that are skimmed from the surface have less than 1% water content, and they gravity drain to the customer’s holding container where they can be disposed of using the correct and approved disposal method.
Reduce Waste & Boost Productivity
For over 38 years, EdjeTech Services has engineered advanced fluid filtration and recycling solutions for machining and metalworking industries.
Our systems increase uptime, cut costs, extend fluid life, and improve efficiency. Discover how we can optimize your operations today.
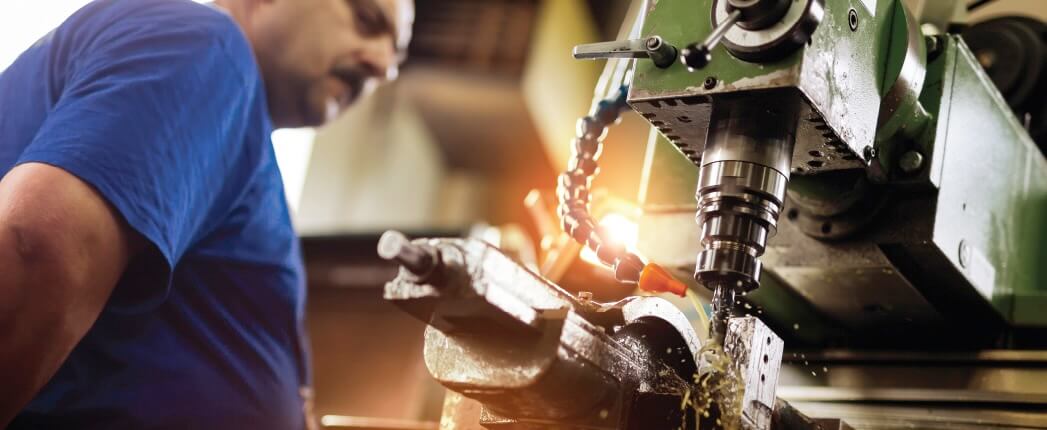