Centralized Coolant Filtration Systems
Explore EdjeTech’s range of Central Coolant Filtration Systems, engineered to revolutionize coolant management in machine shops and industrial settings. Our systems, including the innovative C.R.O.S.S and TMCRS, are designed to optimize the lifecycle of coolants, enhance machine performance, and drive cost-effectiveness.
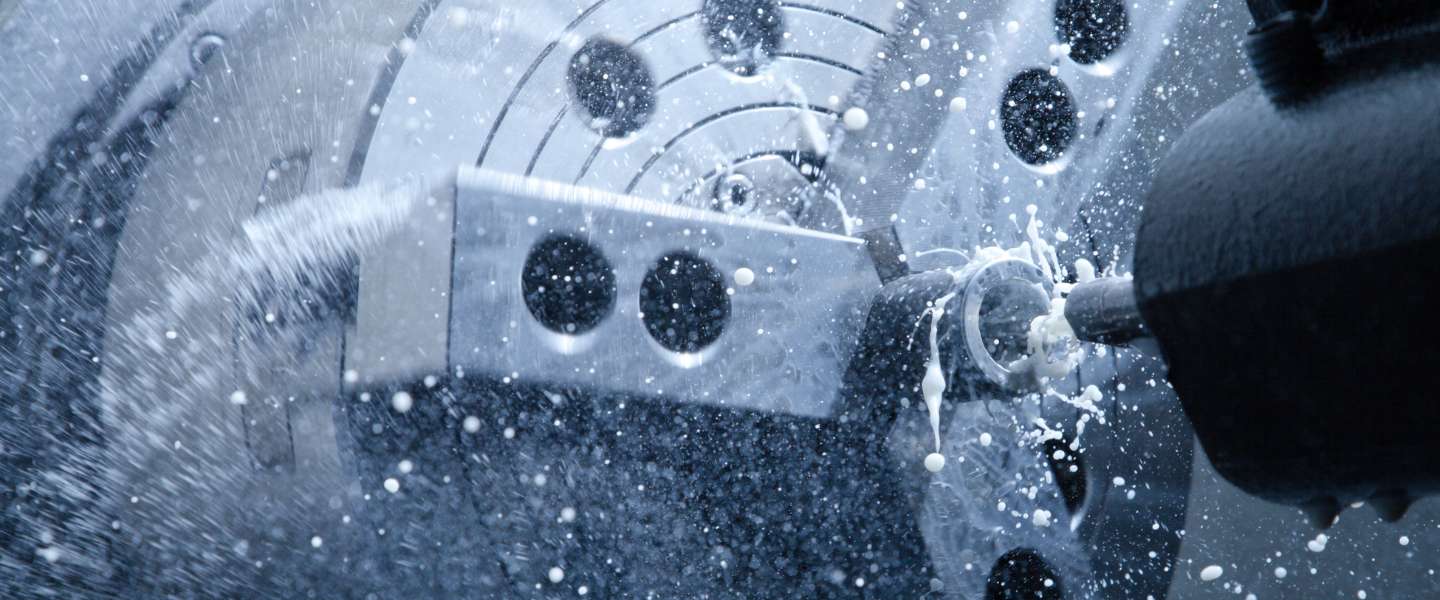
Centralized Coolant Management
EdjeTech’s Central Coolant Filtration Systems, including the C.R.O.S.S. and TMCRS models, are engineered to meet the rigorous demands of high-performance industrial environments. These environments include metalworking industries such as CNC operations, machine shops, steel milling, and tube milling. Key features of these systems include:
Supply and Recycling of Coolants:
- Designed to efficiently supply and recycle coolants to multiple CNC machines through piping networks
- Suitable for various shop sizes, flow rates, and configurations
Efficient Particulate and Contaminant Removal:
- Incorporates modular magnetic separators, paper bed filters, and tramp oil separators for your unique requirements
- Significantly reduces tramp oil to below 1/4 of 1% by volume, optimizing coolant lifecycle and operational efficiency
Our innovative filtration technology is more than just contaminant removal; it's a strategic tool in enhancing tool longevity, part precision, and overall production quality. These systems are instrumental in driving down operational costs, reducing downtime through automated features, fostering extensive coolant reuse, and meeting stringent environmental standards.
EdjeTech's solutions stand out for their adaptability to diverse manufacturing settings and their ability to integrate seamlessly into various shop layouts. They go beyond the conventional role of filtration systems, acting as pivotal partners in your production line. Each system is calibrated and tested to ensure peak coolant performance, reinforcing your commitment to precision, sustainability, and cost-effective manufacturing practices.
Centralized Systems
The variety of systems listed below all have the option to be designed and manufactured using a centralized design for your facility. The benefits of a centralized design is increased automation for your fluid recycling waste stream. Our systems are all modular with a variety of add-on features designed to filter the contaminants typical to your fluid waste stream. Our design team will work closely with you to deliver a system customized to your facility's flow-rates, desired purity levels (PPM), automation features, fluids types, and more.
Coolant Filtration System
Designed for CNC and general machining, this automated system filters and recycles coolants in space-constrained facilities, serving from single to multiple machines with comprehensive contaminant removal.
Tube Mill Filtration System
A specialized and centralized design for tube milling facilities. Modular, scalable, and adaptable to any facility size. Filters all forms of tramp oil, metals, and other contaminants to keep your coolants pristine.
Features
- High-Efficiency Filtration: Removes fine particulates, chips, and contaminants, ensuring clean and effective coolant for machining processes
- Automated Self-Cleaning Mechanism: Reduces downtime and maintenance needs, enhancing production efficiency
- Modular and Scalable Design: Allows customization and easy expansion to accommodate growing or changing production needs
- High-Volume Processing Capability: Ideal for facilities with multiple CNC machines or extensive tube milling operations
- Advanced Contaminant Detection and Monitoring: Features sensors and monitoring systems to continuously assess coolant quality and detect contamination
- User-Friendly Interface: Easy-to-use controls for adjusting settings and monitoring system performance
- Compact Footprint: Efficiently designed to maximize space utilization in industrial & machine shop environments
- Durable and Robust Construction: Heavy-duty steel construction to withstand the rigors of industrial use
- Automated Chemical Dosing: Maintains coolant quality by automatically adding necessary additives and treatments
- Temperature Regulation: Keeps coolant at optimal temperatures for consistent machining performance
- Multi-Stage Filtration Process: Thoroughly removes a wide range of contaminants such as metal chips, tramp oil, and more to maintain coolant integrity
- Eco-Friendly and Sustainable: Promotes recycling and reduces waste, aligning with environmental sustainability goals
- Seamless Integration with Existing Systems: Can be integrated with current machining and control systems for streamlined operations
- Enhanced Safety Features: Includes built-in safety mechanisms to protect operators and the facility
Servicing Diverse Industries & Applications:
- Metalworking
- CNC Milling
- CNC Turning & Lathing
- CNC Grinding
- CNC Machining
- CNC Drilling
- CNC Tapping & Threading
- OEM Manufacturers
- General Manufacturing
Reduce Waste & Boost Productivity
For over 38 years, EdjeTech Services has engineered advanced fluid filtration and recycling solutions for machining and metalworking industries.
Our systems increase uptime, cut costs, extend fluid life, and improve efficiency. Discover how we can optimize your operations today.
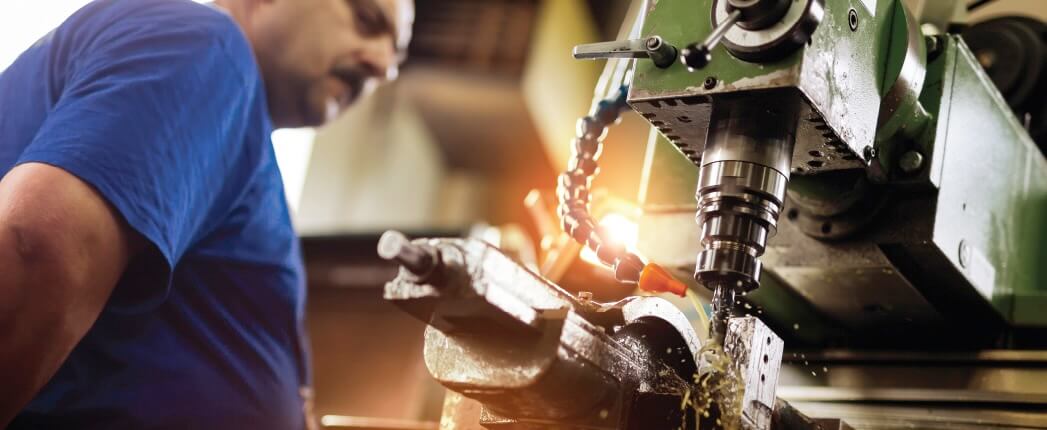